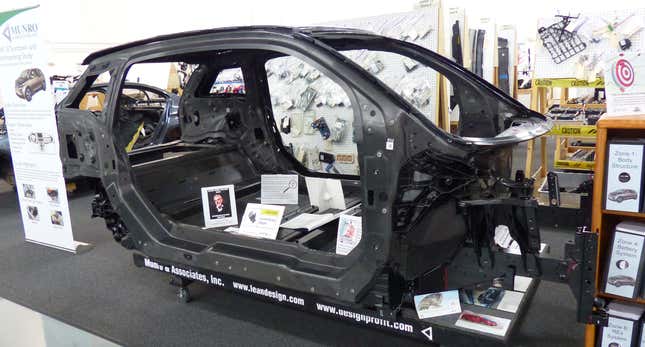
Ever wonder how much air vents cost on a Honda versus a Toyota, or how much a horn bracket weighs on a BMW? Unless you’re the most deeply obsessive car enthusiast in the world, probably not. But automakers care, and they’re always trying to figure out ways to outdo competitors—even at the tiniest level. Meet the company that tears down entire cars to help do that.
All automakers “cheat” off each other. They buy their competitors’ cars, disassemble them, and learn precisely how they work and how they’re made. This reverse engineering is called “competitive benchmarking,” and while sometimes it’s done in-house, there are also entire companies devoted to the practice. One of them is Munro and Associates, a firm of manufacturing experts contracted by OEMs and suppliers to tear down cars and car parts to the very last nut and bolt.
Imagine a place where auto engineers can check out parts of competitors’ cars like they’re library books. And where they can participate in deep-dive lectures on how other companies build vehicle systems, how the systems work, and how much they cost to make. That’s what Munro does.
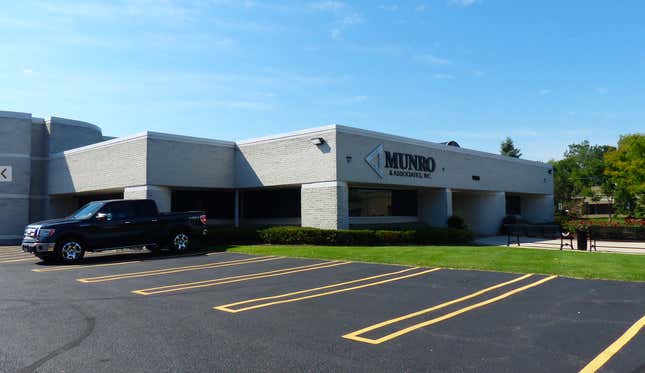
Of course, there are some automakers out there who have their own internal labs for analyzing competitors’ cars, but Munro is a huge player in the industry, with multiple facilities teaching scores of companies the intricacies of automotive manufacturing, helping them learn about the competition and saving them time and money on their own future designs. Munro can do these kinds of teardowns more cheaply and effectively because it’s all they do. But not a ton of people outside the car industry know that they exist, or why they are necessary.
I stopped by Munro’s headquarters in Auburn Hills to take a look at what the company does, and was greeted by a building filled with completely— and I mean completely—dismantled automobiles, including that BMW i3 up top.
“Costing”
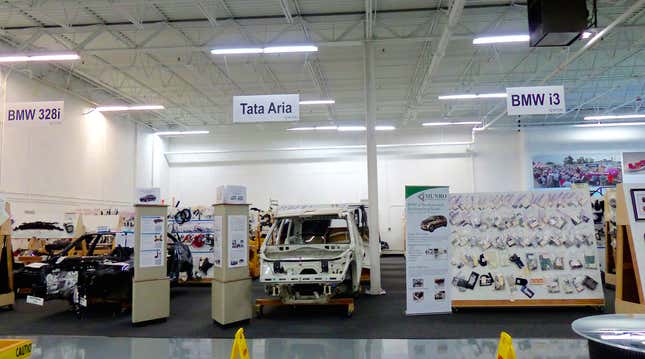
Munro tore that i3 into its more than 54,000 (that’s 31,000 mechanical, 23,000 electrical) individual parts, analyzing all of them for weight, cost, and manufacturing time needed, resulting in a 23,000 page report sold to automakers interested in learning the most minute of details of BMW’s plug-in hybrid electric city car.
If you don’t believe me when I say the company analyzed 54,000 parts, here’s a shelf filled with analyses of every part in the car, organized into different “zones.”
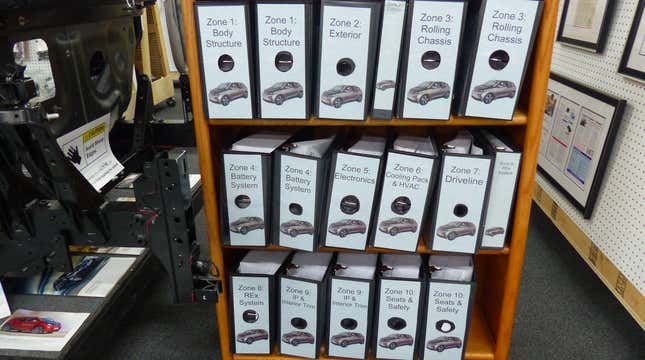
And these analyses don’t just include major components—it’s literally every single part, including fasteners. Here’s a look at just one of the books:
And here are two randomly-chosen pages from the enormous report. Want to know how much it costs BMW (or, more likely, its supplier) to make a horn bracket? Of course you do!
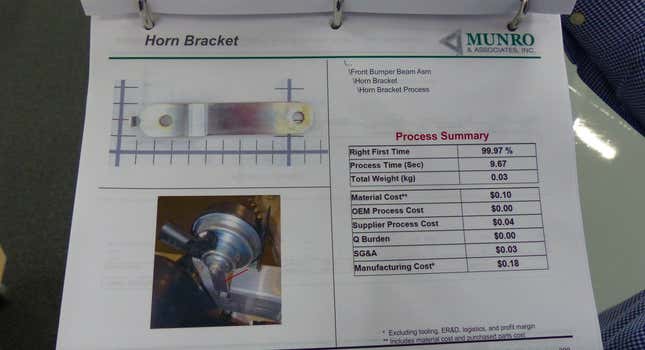
According to Munro, the horn bracket weighs 0.03 kg, and takes about 10 seconds to make for a paltry 18 cents.
And if that bracket isn’t exciting enough, you’re almost certainly chomping at the bit to learn how much it costs to make one of BMW’s fuse buss assemblies for its high voltage battery pack, and it looks like that 0.01 kg part is a whopping 89 cents that takes 39 seconds to build.
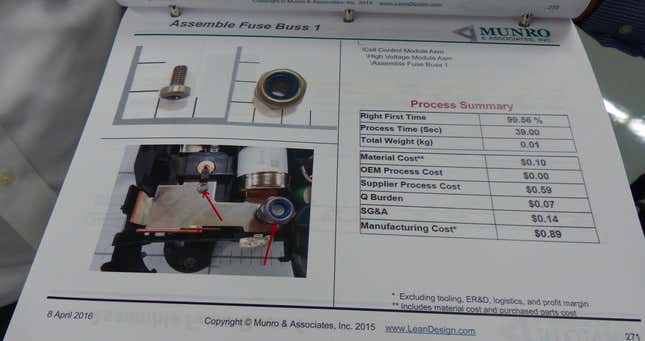
Sometimes a competitor interested in a certain vehicle buys that car for Munro to tear down. In other cases, Munro will buy it to sell the findings. The latter was the case with the i3.
How Munro comes up with these cost figures involves a lot of computerized modeling and expertise from people with decades of manufacturing experience.
That modeling can be visually depicted as a cost map, shown below. The cost map is essentially a second-by-second breakdown of the car’s—and its components’—exact manufacturing processes. Cost maps for entire cars are enormous, and—according to engineers at Munro—can span hundreds of yards in length when printed out. In the case of the i3, there were 196,000 manufacturing steps in total.
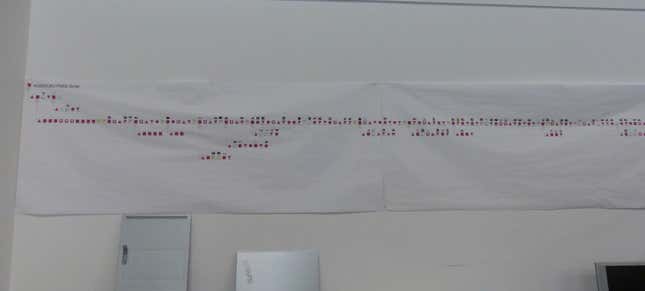
A closer look at this cost map reveals just how detailed Munro’s costing process is. It includes steps like “snap together,” “push on connector,” “twist wire,” “screw drive,” “turn assembly on” and other seemingly mundane—yet still time consuming—parts of the manufacturing sequence.
Each step has a time associated with it; Snap together, for example, takes one second, while “push on connector” takes two and “position lug” takes five.
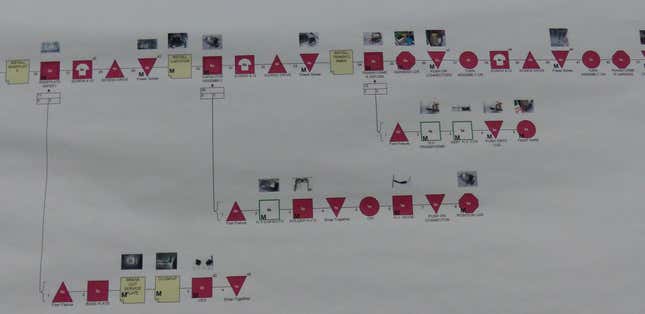
In the end, the cost model shows how the car and its components are manufactured, and results in a report that accounts for everything from material cost to tool burden—which considers things like floor space required for certain tools, electricity to run those tools, and tool maintenance costs— to burden rate, which depends largely on labor costs associated with the countries in which the parts are made.
To come up with the right numbers, Munro has to know exactly which materials are used. Figuring that out part isn’t always simple, either. Sometimes bearings have exotic grades of steel, for example. So Munro might have to send out a sample to a lab to figure out the grade.
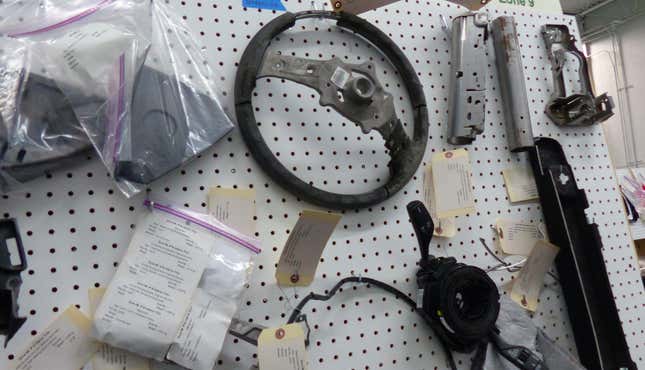
Munro also has to know how much of each component is made of each material to get an accurate cost. Take this BMW steering wheel above, which Munro had to cut into to figure out what and how much metal lies below the plastic cover.
For labor costs, it’s also not always straightforward figuring out where parts are made, either. Sure, it’s sometimes stamped into the part or there’s a sticker, but other times Munro either has to do research to figure out a part’s origin, or they just know where it’s made based on similar parts they’ve seen on other vehicles.
If you want the full report on that i3 I mentioned, it’ll cost you $150,000.
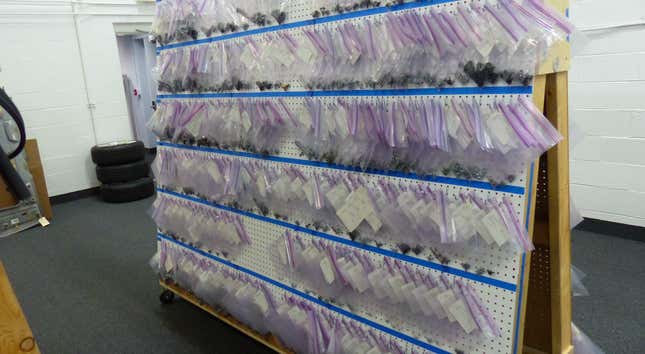
How It Works
Baffled by how the company can have this kind of precision in their cost models, I sat down with Munro’s engineers to learn more.
They gave me an example of an instrument panel, saying they know it’s made of a certain type of plastic, requires a certain size tool (they also said the tool might require “slides” if there are special features involved) that takes a certain amount of money and time to operate , and the manufacturing sequence requires a certain amount of time to cool.
They know these things, they say, because they’ve done tons of research and built on decades of manufacturing experience from employees with backgrounds in various manufacturing and engineering disciplines.
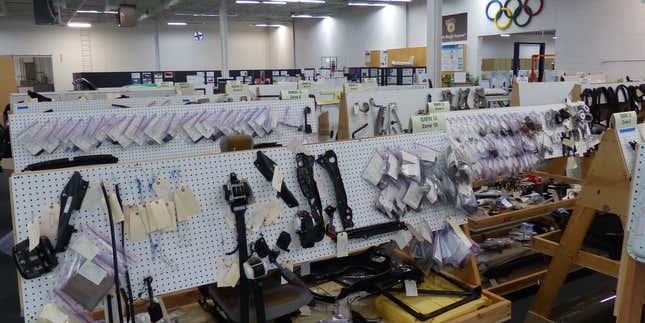
I could tell the engineers I spoke with knew what they were talking about, as they could seemingly visualize how an instrument panel is made, waving their hands up and down trying to emulate the movement of the machines that turn a giant piece of plastic into a precisely formed dashboard.
Plus, the engineers told me, the cost models are proven. Some manufactures, they said, actually hand their own parts to Munro asking them to use their model to see how close they can get to the actual cost of manufacture. Munro says their numbers always come very close, and that they’ve even been accused of having insider information.
You Can Have Whatever You Like
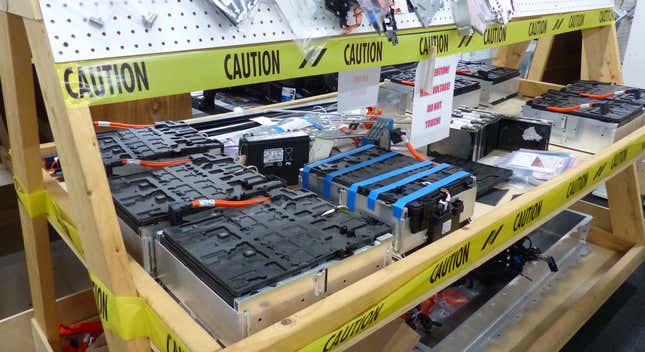
But costing is only a part of what Munro does. A big part of what they offer to car companies is engineering expertise, holding detailed workshops for car companies to teach engineers how other companies are designing certain systems.
Let’s say a company interested in electrification might buy Munro a Tesla Model S. So Munro tears it down and invites engineers at that company to a series of workshops on various vehicle systems. One day, people from that company’s electrified powertrain team might attend a workshop on the Tesla’s battery pack. Or maybe people from the cooling system might show up to learn how Tesla keeps its cells and motors from overheating.
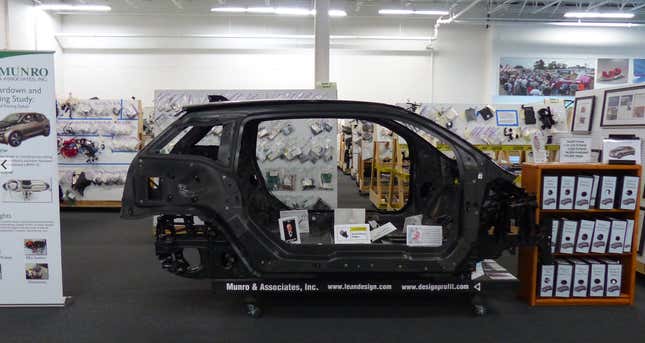
And the workshops aren’t just basic “here’s how this is built” presentations. Munro actually analyzes the systems and tries to answer complex questions like, for example, what Mazda does at a system level to give their 3 such good handling for its class. In some cases, they even send parts out to have them tested for strength of even waterproofness.
But one of the coolest things about Munro is the facilities are filled with torn-down car parts, all of which can be checked out like a library book for engineers to study and, if they want to, scan into their own CAD software for further analysis. That might sound like cheating, but that’s how engineers learn and stay current—SAE conferences aren’t always enough.
Want a piston? Sure. Want to study BMW’s seat foam? Why not? Hell, here’s the sound-deadening fiberglass found in the BMW i3's muffler. It turns out there is 0.311 kg of fiberglass in there. Some muffler engineer out there might find that to be useful.
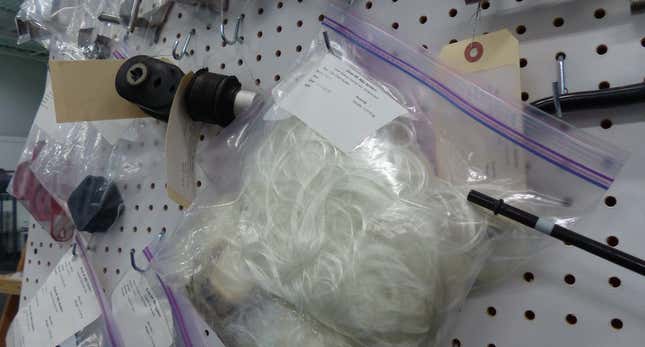
They had to disassemble the muffler to figure out what materials are inside and how much it costs to build the thing, as well as how it’s done— it all goes into that big, quarter-mile long costing map.
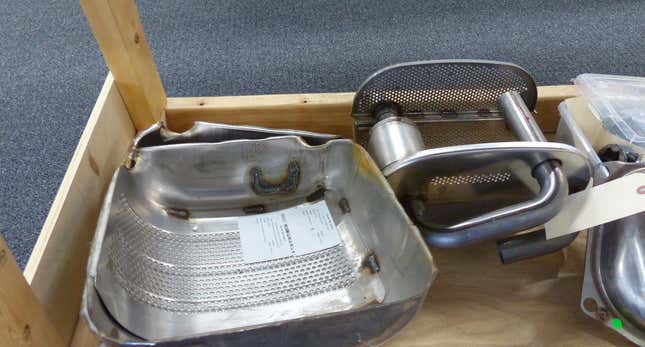
And if I still haven’t communicated just how far Munro actually takes this whole teardown thing, check this out: on the right is a wheel hub. It connects your suspension to your wheel, and normally, car manufacturers just buy that whole thing as an assembly.
But Munro didn’t just write “Hub Assembly: $50,” they actually tore into the assembly itself, cutting into the bearing surfaces to figure out exactly what materials comprise this hub, and how it’s all made.

Next, here are all the brake parts off the BMW i3:

Again, Munro didn’t just count the caliper assembly as one part, they tore it into its basic components: brackets, piston, bolts, etc— some of which are bagged, and all of which are tagged with information about what material comprises them is and how much they weigh.
Why Else Do Companies Need This Kind Of Detail?
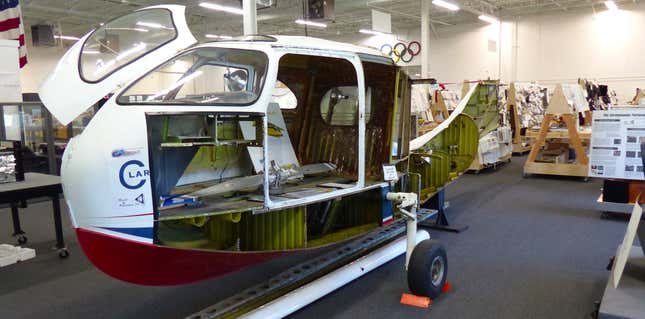
Munro isn’t just there to help engineers learn about how the competition designs and assembles its cars, it’s also there to help automakers—who really should be called “auto assemblers”—figure out if they’re getting ripped off by their parts suppliers.
Knowing exactly how much it costs to build a wheel bearing, for example, can act as leverage for negotiation against a supplier of that part. At the same time, suppliers also go to Munro to learn. If, for example, one of their competitors is selling a part for what seems like impossibly too little, the supplier might ask Munro to tear it down and figure out how the competitor is saving cost.
And Munro does costing, benchmarking and even quality predictions for many different industries, not just automotive. That plane above is a Republic Seabee RC-3, which Munro says incorporated a “minimalist approach to Aircraft structural design,” making it a great way for Munro’s engineers to learn more about lightweight design.
Besides automotive and aerospace, Munro has worked with clients from the defense, marine, medical and the electronics industries. You name it, and Munro’s engineers tear it apart.
They even did analyses on rice-cookers for one company looking to reduce manufacturing costs and increase quality:
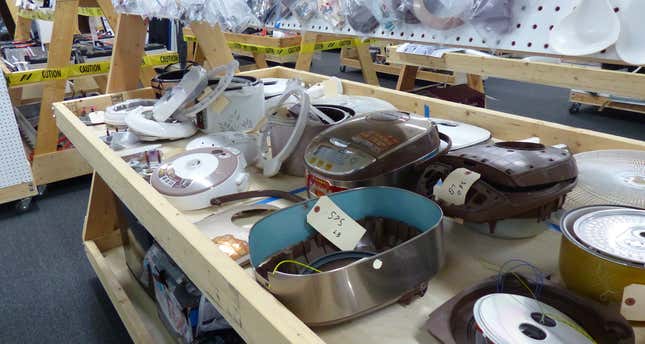
And that’s really their goal: they want to use their general manufacturing knowledge and their understanding of how various manufacturers accomplish certain tasks to help clients become more “lean”—to reduce time to market, to improve quality, to reduce research and development expenses, to reduce engineering and manufacturing costs, and to keep companies competitive.
Those are really the goals of competitive benchmarking in general, and Munro’s facility has demonstrated just to what lengths automakers go to scope out the competition.
Here’s more of what Munro does, particularly that i3:
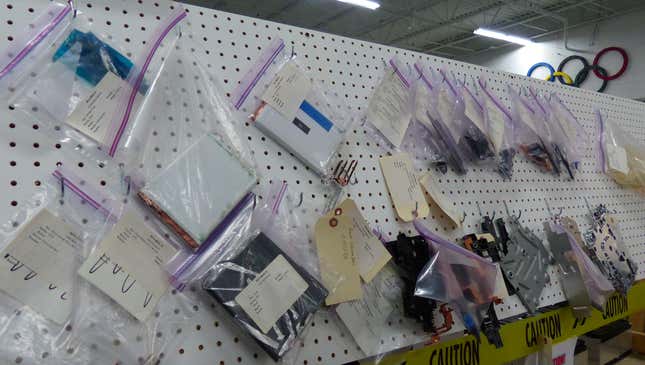
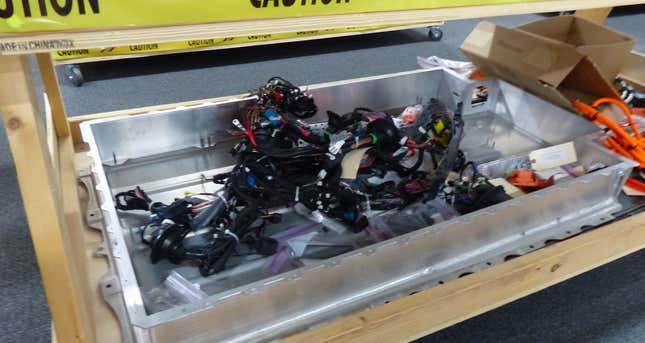
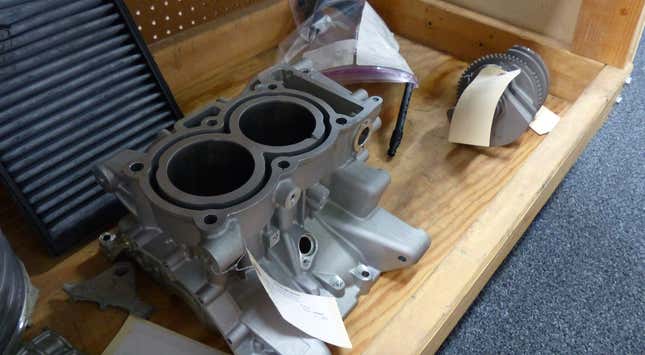
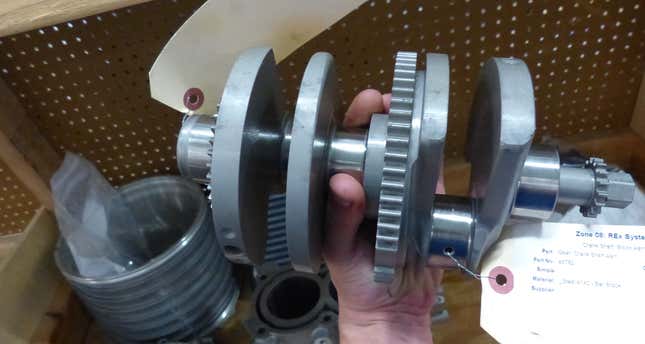
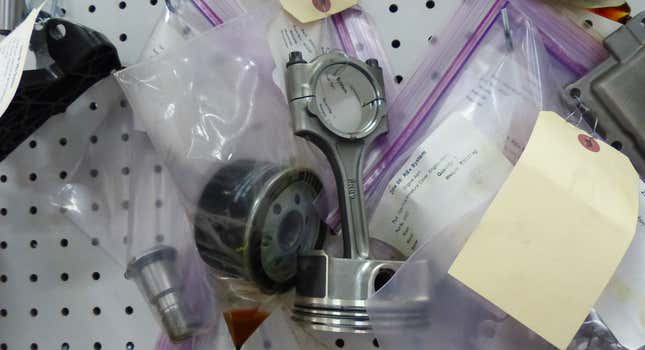
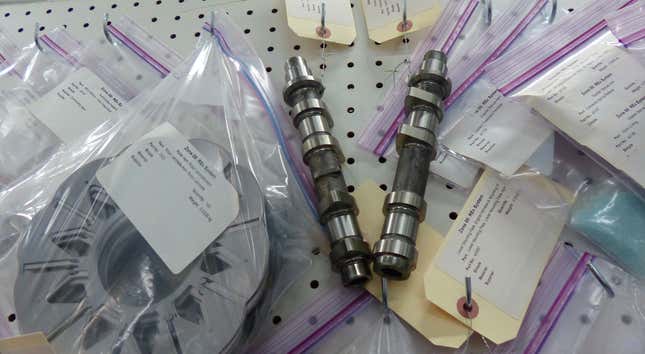
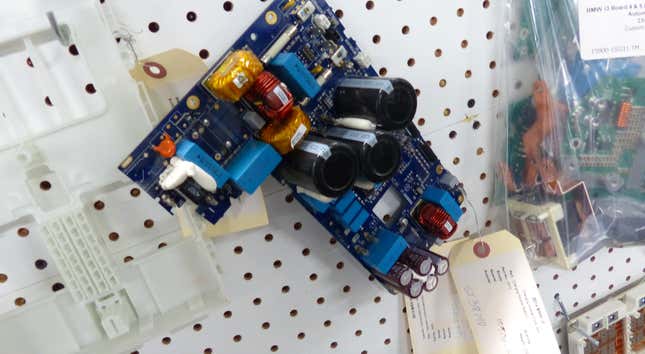
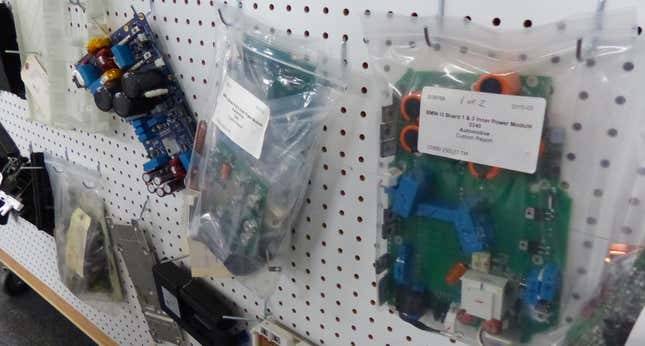
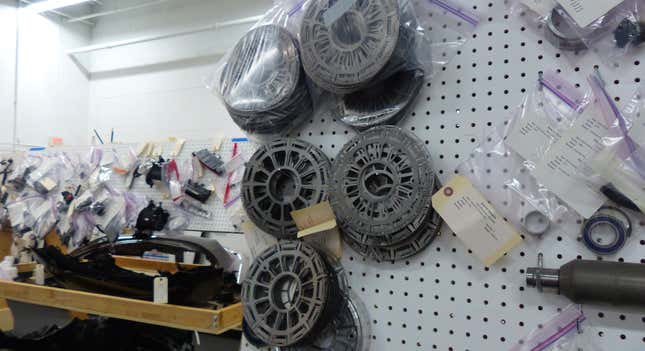
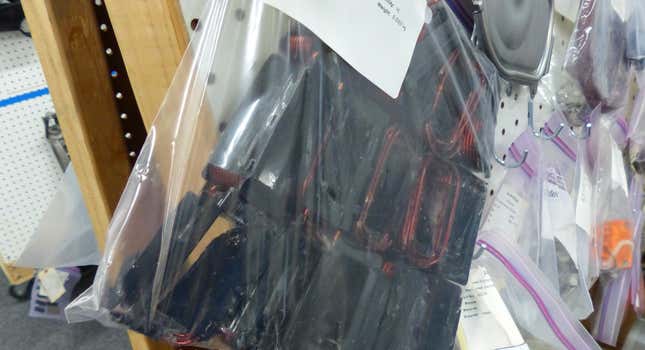
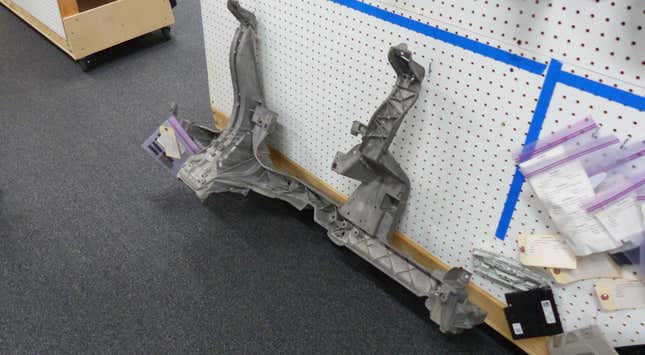
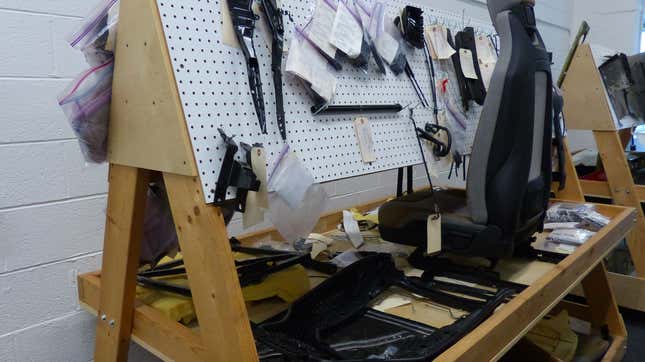
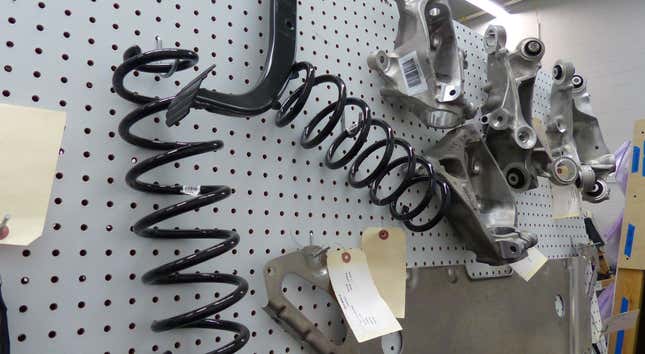
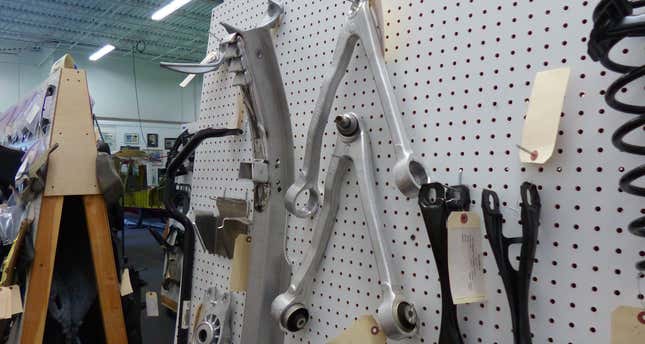
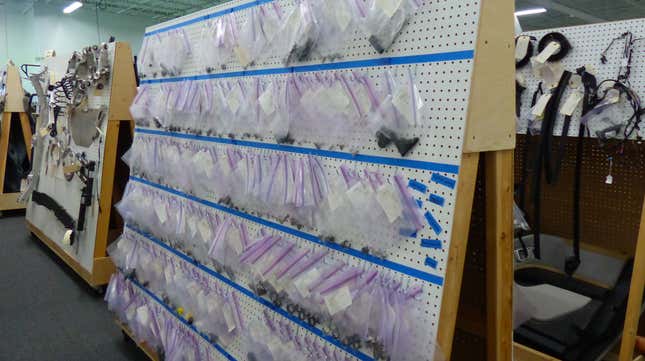
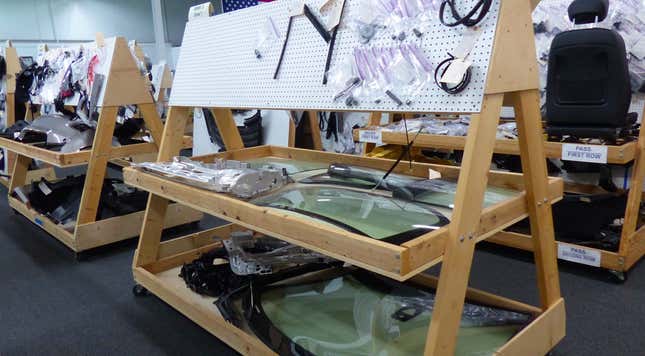
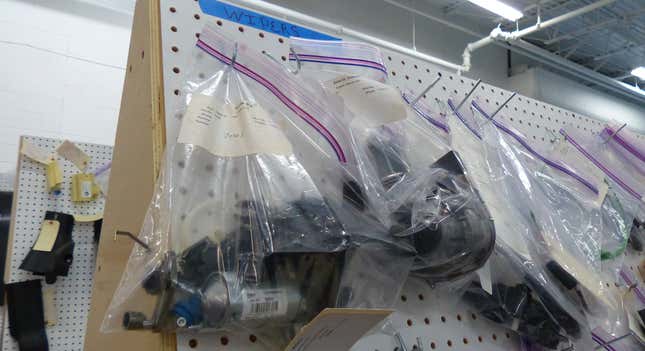
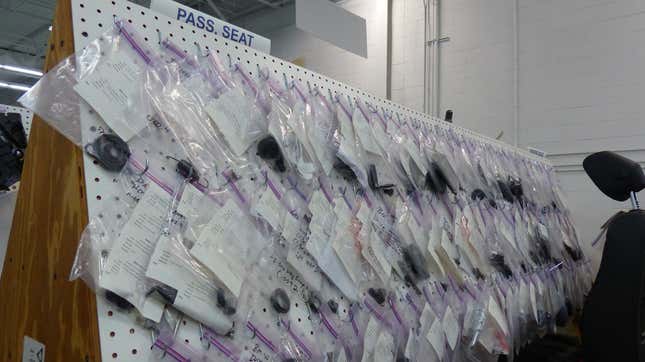
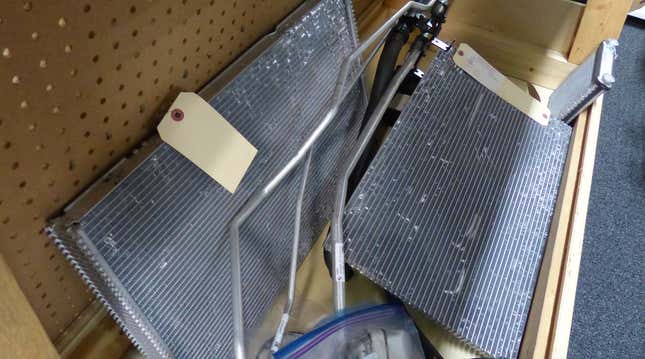
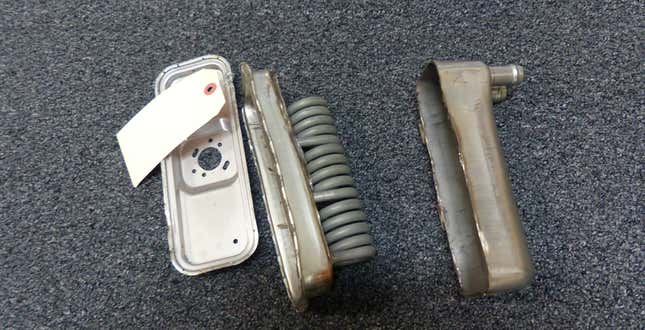
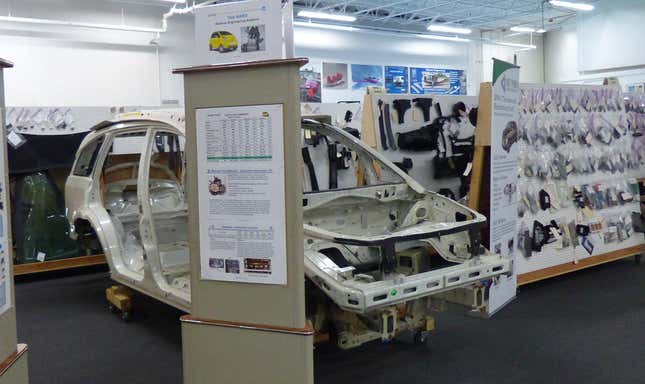
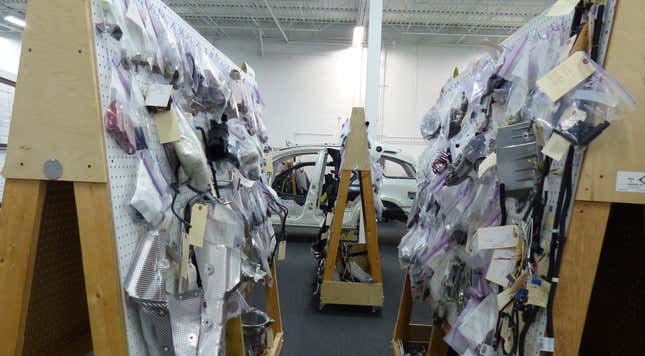
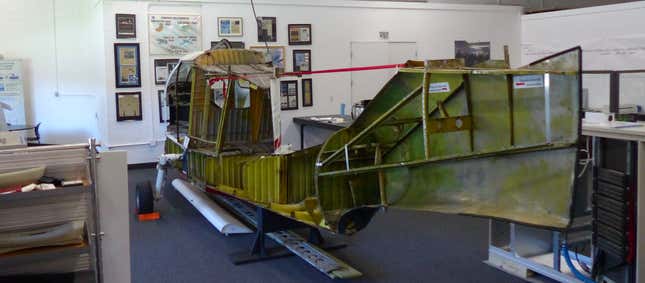
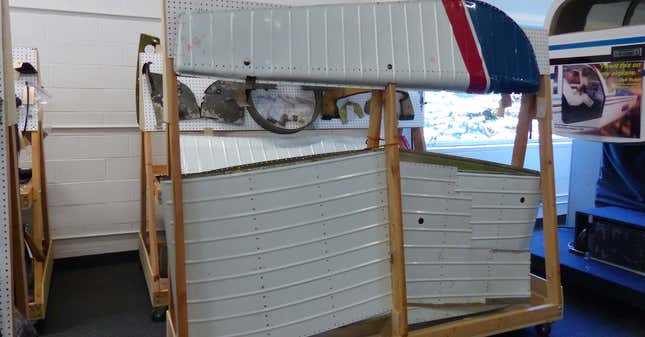
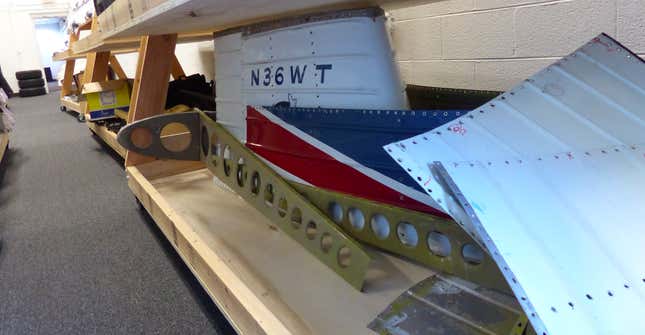
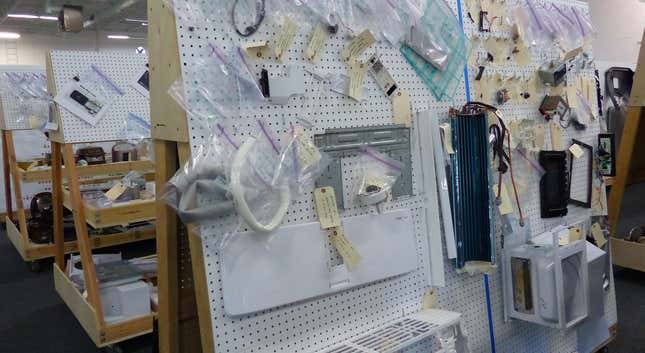